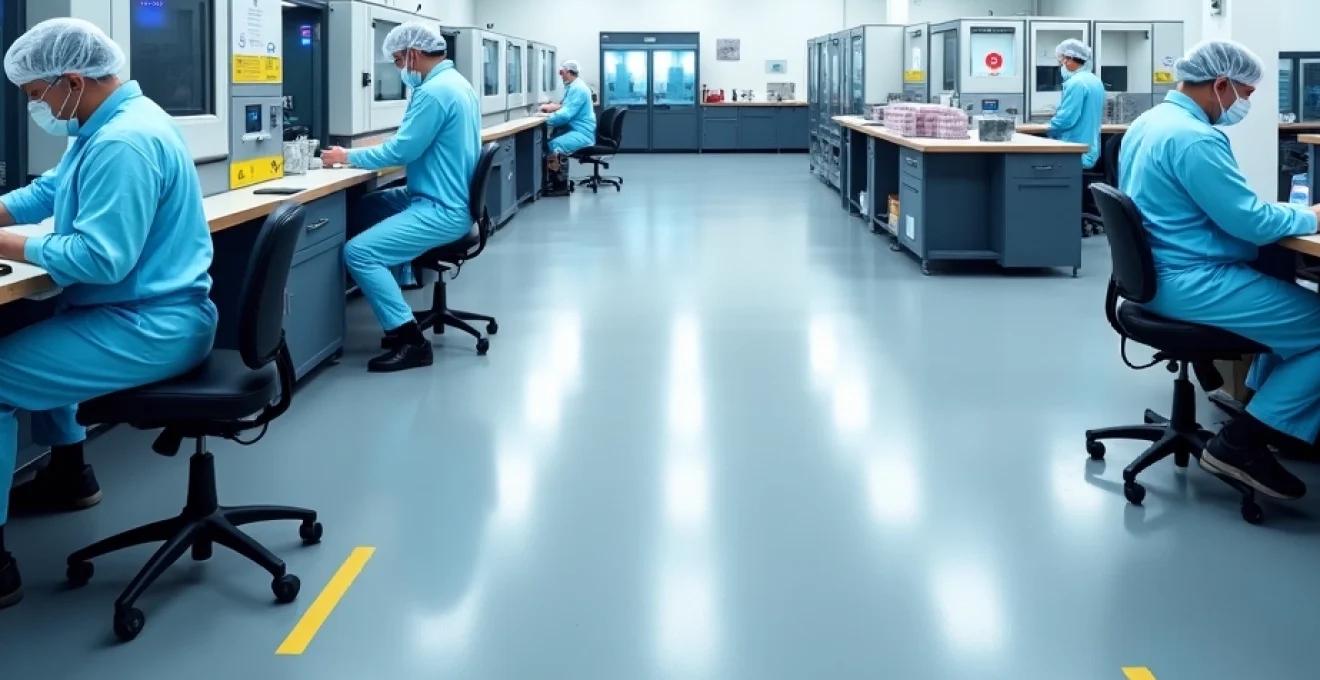
Electrostatic discharge (ESD) poses a significant threat to electronic components during manufacturing processes. With modern microelectronics becoming increasingly sensitive to static electricity, even discharges as low as 10 volts can damage or destroy sensitive components, resulting in substantial financial losses and reliability issues. The implementation of proper ESD protection materials has become a critical aspect of quality control in electronics manufacturing facilities worldwide. From workstation surfaces to packaging materials and personal grounding equipment, a comprehensive ESD control program requires careful material selection based on electrical properties, durability, and compliance with industry standards.
Statistical analysis reveals that ESD-related failures account for approximately 25-30% of all electronic device failures, with damages costing the electronics industry billions of dollars annually. Manufacturing facilities implementing robust ESD protection programs typically report 60-70% reduction in component failure rates and significantly improved product reliability. Beyond immediate component failure, latent damage from sub-threshold ESD events presents an even more insidious threat, potentially leading to premature field failures that damage brand reputation and customer confidence.
Fundamentals of ESD protection materials in electronics manufacturing
The core principle behind ESD protection materials is their ability to safely manage static electricity through controlled conductivity. Unlike standard insulators that trap charges or conductors that allow rapid discharge, ESD materials provide a controlled path for static dissipation, preventing dangerous charge accumulation while avoiding sudden discharges that could damage sensitive components. This controlled conductivity is measured in terms of surface resistivity (ohms per square) or volume resistivity (ohm-centimeters), with materials typically classified into conductive (10^3 to 10^5 ohms/square), static dissipative (10^5 to 10^12 ohms/square), and insulative (>10^12 ohms/square) categories.
Material selection depends heavily on the specific application within the manufacturing environment. For example, work surfaces typically utilize dissipative materials to safely drain static charges while preventing rapid discharge events. Meanwhile, grounding systems may incorporate more conductive materials to ensure efficient charge equalization. The electrical properties of these materials are often achieved through specialized additives or surface treatments that modify standard base materials to provide the desired level of conductivity.
A properly designed ESD control program combines multiple layers of protection, with each material playing a specific role in maintaining a static-safe environment. The integration of these materials creates a complete system rather than isolated solutions.
Temperature and humidity significantly influence the performance of ESD protection materials. Most ESD control programs specify maintaining relative humidity between 40-60% to facilitate natural static dissipation through surface moisture. However, many modern manufacturing processes, particularly in semiconductor fabrication, require strictly controlled low-humidity environments, making humidity-independent ESD materials increasingly important. These specialized materials maintain their protective properties across wide environmental ranges, ensuring consistent protection regardless of ambient conditions.
Beyond electrical properties, manufacturers must consider chemical compatibility, particle generation, outgassing characteristics, and mechanical durability when selecting ESD materials for electronics production. This is especially critical in cleanroom environments where material degradation or contamination could compromise both ESD protection and product quality. Advanced materials incorporating specialized polymers, carbon nanotubes, or inherently dissipative polymers represent the cutting edge of ESD protection technology development.
Conductive and dissipative materials for ESD control
The distinction between conductive and dissipative materials represents a fundamental concept in ESD protection. Conductive materials, with surface resistivity below 1 × 10^5 ohms/square, provide rapid charge equalization but can potentially cause damaging discharge events if not properly implemented. Dissipative materials, ranging from 1 × 10^5 to 1 × 10^12 ohms/square, offer a controlled pathway for static charges to dissipate gradually, making them ideal for most workstation surfaces and handling equipment. This balanced approach allows for effective static control while minimizing the risk of damaging discharge events.
Material selection should follow the "ground-up" principle of ESD control, starting with properly grounded conductive or dissipative flooring systems connected to personnel via appropriate footwear. This continues upward through workstation surfaces, tools, containers, and ultimately extends to the personal grounding of operators handling sensitive components. The integrated system approach ensures continuous pathways for static dissipation while preventing charge generation and accumulation throughout the manufacturing process.
Recent advancements in permanent anti-static materials have introduced intrinsically dissipative polymers (IDPs) that maintain their ESD properties throughout the material's lifetime. Unlike topical treatments that can wear off or be removed by cleaning, these materials offer consistent, long-term protection. Many facilities are transitioning to these advanced materials despite their higher initial cost, recognizing the long-term value in reduced maintenance and more reliable protection.
Carbon-loaded polymers and their application in ESD workstations
Carbon-loaded polymers represent one of the most widely implemented ESD protection technologies in electronics manufacturing workstations. These materials incorporate carbon particles dispersed throughout a polymer matrix, creating conductive pathways that allow controlled static dissipation. The electrical properties can be precisely engineered by adjusting carbon concentration and particle size distribution, allowing manufacturers to create materials with specific resistivity ranges tailored to particular applications.
Workstation mats typically utilize carbon-loaded rubber or vinyl with surface resistivity in the 10^6 to 10^9 ohms/square range. This provides sufficient conductivity to dissipate static charges while preventing rapid discharge events that could damage components. More advanced formulations incorporate multiple layers with different resistivity profiles, creating a gradient effect that offers improved charge control while maintaining durability under heavy use conditions.
Manufacturing considerations for carbon-loaded polymers include ensuring homogeneous carbon distribution throughout the material to prevent "hot spots" of excessive conductivity or insulative regions that could trap charges. Quality control testing typically includes point-to-point resistance measurements across multiple locations to verify consistent electrical properties throughout the material. Long-term performance testing has demonstrated that properly formulated carbon-loaded polymers can maintain their ESD properties for 5-10 years in typical manufacturing environments when properly maintained.
Metal-filled composites: conductivity ratings and selection criteria
Metal-filled composite materials offer an alternative approach to achieving controlled conductivity for ESD protection. These materials incorporate metal particles such as nickel, copper, silver, or aluminum within a polymer matrix. Compared to carbon-loaded materials, metal-filled composites can achieve higher conductivity levels (as low as 10^3 ohms/square) while maintaining flexibility and formability. This makes them particularly valuable for applications requiring both high conductivity and complex geometries, such as customized component carriers or test fixtures.
Selection criteria for metal-filled composites should consider not only the initial electrical properties but also long-term stability under exposure to manufacturing chemicals, cleaning agents, and mechanical wear. Materials utilizing nickel or silver fillers typically offer superior corrosion resistance compared to copper or aluminum alternatives, making them preferred for environments with exposure to humidity or corrosive chemicals. The particle size, shape, and distribution significantly impact both electrical performance and mechanical properties, with smaller, flake-shaped particles typically providing more efficient conductive networks at lower fill rates.
An important consideration when implementing metal-filled composites is their potential for galvanic corrosion when in contact with dissimilar metals. This can be mitigated through proper material pairing and the use of appropriate barrier layers in multi-material assemblies. The cost of these materials varies significantly based on the metal filler used, with silver-filled composites commanding premium prices while providing superior conductivity and chemical resistance compared to alternatives.
Static dissipative flooring systems: vinyl, epoxy, and urethane options
Flooring systems represent the foundation of comprehensive ESD control programs in electronics manufacturing facilities. Static dissipative flooring typically aims for surface resistivity between 10^6 and 10^9 ohms/square, providing effective charge dissipation while ensuring personnel safety by limiting current flow. Three primary options dominate the market: vinyl tile systems, epoxy coatings, and urethane formulations, each offering distinct advantages for specific manufacturing environments.
Vinyl tile systems offer relatively simple installation and maintenance, with modular designs allowing for easy replacement of damaged sections without disrupting production. Modern formulations incorporate carbon or conductive fiber networks throughout the material thickness, ensuring continued protection even as the surface experiences wear. These systems typically maintain effective ESD properties for 7-10 years before requiring replacement, making them cost-effective for many facilities despite their relatively soft surface compared to alternative options.
Epoxy flooring systems provide superior chemical resistance and durability, making them ideal for environments with heavy equipment traffic or exposure to harsh chemicals. These systems typically incorporate conductive additives within a multi-layer application process, creating a seamless surface that eliminates joints where dirt or moisture could accumulate and compromise ESD performance. Performance testing indicates that properly installed epoxy systems can maintain their ESD properties for 10-15 years in typical manufacturing environments, offsetting their higher initial installation cost.
Urethane flooring represents the premium option for critical manufacturing environments, offering exceptional impact resistance, flexibility, and chemical resistance. These systems typically incorporate specialized conductive polymers within their formulation to provide consistent electrical properties throughout the material's lifetime. While carrying the highest initial cost among flooring options, their extended service life of 15-20 years and superior performance characteristics make them the preferred choice for advanced semiconductor manufacturing facilities where production downtime for flooring maintenance carries substantial financial implications.
Conductive fabric technologies in clean room environments
Clean room environments present unique challenges for ESD protection, requiring materials that provide effective static control while minimizing particle generation and contamination risks. Conductive fabric technologies have emerged as a critical solution for this specialized environment, offering adaptable protection for both personnel garments and environmental surfaces. These fabrics typically incorporate conductive fibers such as carbon, stainless steel, or silver in a grid or yarn structure interwoven with polyester or nylon base materials.
The grid density and conductive fiber selection significantly impact both ESD performance and cleanroom compatibility. Fabrics utilizing continuous carbon fibers typically offer more reliable electrical properties compared to discontinuous or staple fiber alternatives, maintaining performance even after repeated laundering cycles. For ISO Class 1-3 cleanrooms, monofilament conductive yarns are preferred over multifilament alternatives due to their reduced particle shedding characteristics, despite their typically higher cost and somewhat reduced flexibility.
Recent innovations in conductive fabric technology include hydrophobic treatments that maintain ESD performance in varying humidity conditions while improving contamination resistance. Testing protocols for these materials must evaluate both initial and post-laundering electrical properties, with premium materials maintaining surface resistivity within 20% of initial specifications after 100+ standard laundering cycles. For mission-critical applications , continuous monitoring systems can be integrated into conductive fabrics, providing real-time verification of grounding integrity throughout manufacturing operations.
Anti-static packaging and transport materials
The protection of electronic components extends beyond the manufacturing workstation to include storage and transportation phases where ESD risks remain significant. Anti-static packaging materials employ various technologies to prevent charge generation, dissipate existing charges, and shield components from external electric fields. These materials must balance ESD protection with physical protection, moisture control, and visibility requirements specific to manufacturing and logistics operations.
Packaging materials are typically classified into four categories based on their protective mechanisms: anti-static (low charge generation), dissipative (controlled charge dissipation), conductive (rapid charge equalization), and shielding (field attenuation). A comprehensive packaging strategy often incorporates multiple material types in a layered approach, with inner packaging providing direct component contact protection while outer layers address environmental factors and handling requirements.
Material selection should consider the sensitivity of components being protected, with highly sensitive devices such as MOSFET transistors or CMOS integrated circuits requiring more sophisticated protection compared to less sensitive components. The transportation distance, environmental conditions, and handling procedures also influence packaging requirements, with international shipments typically necessitating more robust protection compared to internal facility transfers.
Metallized shielding bags and faraday cage principles
Metallized shielding bags represent one of the most effective ESD protection solutions for component transport and storage. These bags operate on Faraday cage principles, where a conductive outer layer creates an equipotential surface that attenuates external electric fields by redistributing charges around the exterior surface. This shielding effect can reduce external field strength by 40-60 dB, providing substantial protection against both direct discharge and field-induced charging events that could damage sensitive components.
Modern metallized bags typically employ a multi-layer construction with a metallized polyester or aluminum layer sandwiched between an outer dissipative layer and an inner anti-static layer. The outer dissipative layer (typically 10^8 to 10^10 ohms/square) prevents charge accumulation during handling, while the inner anti-static layer ensures safe contact with sensitive components. The metallized middle layer provides the Faraday cage effect, with aluminum being the most common material due to its excellent conductivity-to-cost ratio.
Quality considerations for metallized shielding bags include seal integrity, puncture resistance, and aging characteristics. Heat-sealed bags provide superior protection compared to fold-over or adhesive-closed alternatives by maintaining a continuous conductive path around the entire package. Advanced manufacturing techniques can now create transparent metallized films that allow visual inspection of contents without compromising shielding effectiveness, albeit at a premium cost compared to standard opaque alternatives.
Pink polyethylene vs. black conductive foam: material characteristics
Component handling within ESD-protected environments often utilizes specialized foams that provide both physical cushioning and electrostatic protection. Two common options are pink polyethylene foam and black conductive foam, each offering distinct protective characteristics suited to different component types and handling requirements. Understanding these differences is essential for implementing appropriate protection throughout the manufacturing process.
Pink anti-static polyethylene foam derives its protective properties from topical anti-static agents that reduce triboelectric charging when components contact the material. With typical surface resistivity in the 10^10 to 10^12 ohms/square range, these materials minimize charge generation rather than providing rapid dissipation pathways. The limited conductivity makes pink foam ideal for storing or transporting components that could be damaged by rapid discharge, such as certain CMOS devices or components with internal capacitance issues.
Black conductive foam incorporates carbon particles throughout its structure, creating a three-dimensional conductive network with surface resistivity typically in the 10^3 to 10^5 ohms/square range. This high conductivity quickly equalizes charges across the material, preventing charge accumulation on inserted pins or leads. However, this rapid equalization can potentially damage extremely sensitive components through current surges if not properly implemented. Black foam is particularly valuable for protecting components with exposed leads or contacts, such as integrated circuits with pin grids or connector assemblies.
Esd-safe totes, containers, and IEC 61340-5-1 compliance
Manufacturing logistics requires specialized containers for moving components between production stages while maintaining ESD protection. ESD-safe totes and containers typically utilize carbon-loaded polypropylene or other conductive polymer formulations to provide durable, reusable protection throughout production environments. These containers must balance electrical properties with mechanical durability, chemical resistance, and cleanroom compatibility as appropriate for specific manufacturing environments.
The international standard IEC 61340-5-1 establishes performance requirements for ESD protective containers, specifying acceptable resistance ranges and testing methodologies. Compliant containers typically feature surface resistivity between 10^4 and 10^11 ohms/square, providing effective charge dissipation while preventing rapid discharge events. The standard also addresses charge generation potential, requiring that containers generate minimal triboelectric charge when in contact with typical materials encountered in electronics manufacturing.
Advanced container designs incorporate features such as conductive dividers for component separation, interlocking mechanisms for secure stacking, and specialized labeling for ESD sensitivity classification. Some systems include integrated humidity indicators or monitoring devices that verify or monitoring devices that verify container conditions throughout transportation and storage processes. Radio-frequency identification (RFID) tagging is increasingly being integrated into premium container systems, enabling automated inventory management while maintaining full ESD protection compliance. For facilities handling moisture-sensitive devices (MSDs), specialized containers incorporating desiccant compartments can simultaneously address both moisture and ESD concerns without compromising protection in either area.
Moisture barrier bags (MBB) for moisture-sensitive devices
Moisture barrier bags (MBBs) address the dual concerns of electrostatic and moisture protection for sensitive electronic components, particularly critical for modern ball grid array (BGA) packages, chip-scale packages, and other moisture-sensitive devices. These specialized bags incorporate multiple protection layers, typically including an outer dissipative layer for ESD protection, a metallized barrier layer that provides both moisture resistance and Faraday cage properties, and an inner anti-static layer for component contact safety. High-performance MBBs achieve moisture vapor transmission rates (MVTR) below 0.02g/m²/day while maintaining ESD protection throughout their service life.
Industry specifications for MBBs follow IPC/JEDEC J-STD-033 guidelines, which define moisture sensitivity levels (MSLs) for electronic components and corresponding packaging requirements. Components rated at higher MSL levels (such as Level 3 or above) require correspondingly higher-performance MBBs with lower MVTR values and more robust sealing systems. The IPC/JEDEC standards also specify shelf life limitations for sealed MBBs, typically ranging from 6 months to 2 years depending on bag specifications and environmental conditions.
Implementation of MBB protection requires careful process control, including monitoring of factory floor exposure time, proper sealing validation, and humidity indicator card (HIC) verification. Advanced MBB systems now incorporate features such as transparent windows for HIC reading without opening bags, tear-notches for controlled opening, and multi-compartment designs that allow partial access without exposing all components to ambient conditions. When properly implemented, MBB packaging extends the floor life of moisture-sensitive components from hours to years, significantly improving manufacturing flexibility while reducing waste from expired components.
Personal grounding equipment and wearables
The human body represents one of the most significant sources of electrostatic charge in manufacturing environments, capable of generating potentials exceeding 15,000 volts under typical conditions. Personal grounding equipment provides controlled discharge paths that prevent charge accumulation while protecting both operators and sensitive components. An effective personal grounding strategy combines multiple elements including wrist straps, footwear, and garments working together to maintain the operator at or near the same electrical potential as the handling environment and components.
The effectiveness of personal grounding equipment depends heavily on proper implementation and consistent usage. Continuous monitoring systems have become increasingly common in critical manufacturing environments, providing real-time verification of grounding integrity with both visual and audible alerts when connections fail. These systems typically monitor both the resistance of the grounding path and the presence of the operator within the workstation, eliminating the possibility of disconnected equipment during component handling.
Training and compliance verification represent critical aspects of personal grounding programs, with most facilities implementing daily testing requirements and maintaining test records for quality assurance purposes. The investment in comprehensive personal grounding systems typically yields returns through reduced component damage rates, improved product reliability, and enhanced process control throughout manufacturing operations.
Wrist straps: resistance values and testing protocols
Wrist straps provide the primary personal grounding mechanism in most electronics manufacturing environments, creating a direct electrical connection between the operator and the facility grounding system. These devices typically incorporate a conductive band worn around the wrist connected to a ground point through a current-limiting resistor. Industry standards specify resistance values between 800 kilohms and 1.2 megohms for these systems, providing sufficient conductivity for static dissipation while limiting current flow to safe levels in case of accidental contact with live electrical sources.
Regular testing of wrist straps represents a fundamental element of ESD control programs, with daily verification being standard practice in most facilities. Testing procedures typically measure two key parameters: the resistance from the operator's skin through the wrist band to the ground connection point, and the strength and integrity of the mechanical connection between the wrist band and the operator's arm. Automated test stations streamline this process by simultaneously measuring both parameters and providing clear pass/fail indicators with test records for documentation purposes.
Advanced wrist strap systems incorporate continuous monitoring capabilities that verify ground connection integrity throughout the workday. These systems typically use small voltage signals to monitor the complete ground path in real-time, triggering visual and/or audible alerts when connections fail or resistance values drift outside acceptable ranges. While representing a higher initial investment compared to standard systems, continuous monitoring eliminates the risk of undetected failures between scheduled testing intervals, providing superior protection for highly sensitive manufacturing operations.
ESD footwear: heel straps vs. full sole grounders
ESD footwear complements wrist straps by providing grounding when operators move throughout the facility, maintaining protection beyond fixed workstations. Two primary approaches dominate the market: heel straps that provide conductive paths through the heel area only, and full sole grounders that create conductive paths across the entire foot surface. The selection between these options should consider operator mobility requirements, flooring systems in use, and the sensitivity of components being handled.
Heel straps offer advantages in terms of comfort, ease of application, and compatibility with diverse footwear styles. These devices typically incorporate a conductive rubber element that contacts both the wearer's sock and the floor surface, with an adjustable strap ensuring consistent positioning. With properly designed conductive flooring, heel straps can provide effective grounding with resistance typically between 10⁶ and 10⁹ ohms. However, their effectiveness depends on consistent heel contact with the floor, which may be compromised during certain movements or standing positions.
Full sole grounders provide more consistent grounding by creating conductive paths across the entire foot surface. These systems typically achieve lower resistance values (10⁵ to 10⁷ ohms) compared to heel straps due to their larger contact area with both the operator and floor surfaces. While offering superior protection, particularly for highly sensitive components, full sole grounders typically require specialized footwear rather than adapting to existing shoes. The investment in dedicated ESD footwear typically pays dividends through improved protection reliability and reduced testing complexity compared to adjustable alternatives.
Anti-static garments: polyester vs. carbon-infused fabrics
Anti-static garments play an essential role in comprehensive ESD protection programs by preventing charge generation from clothing movement and dissipating body charges across larger surface areas. Two primary material technologies dominate this space: surface-treated polyester fabrics and carbon-infused fabrics with inherent conductive properties. The selection between these options impacts both initial performance and long-term protection reliability throughout the garment's service life.
Surface-treated polyester garments utilize hydrophilic topical treatments to create temporary conductive pathways across the fabric surface. These treatments attract atmospheric moisture that facilitates charge distribution and dissipation, typically achieving surface resistivity between 10⁹ and 10¹¹ ohms/square under controlled humidity conditions (40-60% RH). While offering lower initial costs compared to alternatives, these garments require careful laundering protocols to preserve their protective properties, with effectiveness typically declining after 50-100 wash cycles as treatments gradually degrade.
Carbon-infused fabrics incorporate conductive carbon fibers within the textile structure, creating permanent conductive networks that maintain performance regardless of laundering or environmental conditions. These materials typically achieve more consistent resistivity values (10⁷ to 10⁹ ohms/square) and maintain performance across wider humidity ranges compared to surface-treated alternatives. While carrying higher initial costs, carbon-infused garments typically maintain their protective properties throughout their mechanical service life (200+ wash cycles), providing lower total ownership costs for high-volume manufacturing operations when considering replacement frequency and consistent protection levels.
Advanced ESD control materials for semiconductor manufacturing
Semiconductor manufacturing presents exceptional challenges for ESD protection due to both the extreme sensitivity of devices (some modern CMOS components can be damaged by discharges below 50 volts) and the stringent environmental controls required for fabrication processes. Advanced ESD control materials for these environments must deliver consistent protection while meeting ultra-high cleanliness requirements, chemical compatibility needs, and operating effectively in low-humidity conditions where natural static dissipation mechanisms become ineffective.
Material innovation for semiconductor applications has led to the development of specialized solutions that achieve previously unattainable combinations of properties. These advanced materials typically command premium prices compared to general-purpose alternatives but deliver critical performance advantages that justify their implementation in high-value manufacturing operations. The rapid evolution of semiconductor devices toward smaller feature sizes and higher integration densities continues to drive innovation in ESD protection materials, with new solutions emerging to address increasingly stringent protection requirements.
Implementation strategies for advanced semiconductor manufacturing typically incorporate multiple protection layers working in concert, from specialized cleanroom construction materials to process-specific handling equipment and environmental control systems. This comprehensive approach addresses the full spectrum of ESD risks while accommodating the unique constraints of semiconductor fabrication processes.
Ionization equipment materials and static neutralization efficiency
Ionization represents a critical technology for semiconductor manufacturing areas where direct grounding of materials or components is impractical. These systems generate balanced streams of positive and negative ions that neutralize static charges without requiring physical contact with charged surfaces. The materials used in ionization equipment significantly impact both neutralization efficiency and potential contamination risks in cleanroom environments.
Emitter points in ionization systems have evolved from simple stainless steel to advanced alloys and semiconductor materials that resist corrosion while minimizing particle generation. Alpha-emitting materials (typically containing small amounts of polonium-210) offer exceptional neutralization performance without requiring external power sources, though their limited service life (approximately 12 months due to radioactive decay) and regulatory complications have limited their adoption to specialized applications. Modern systems typically utilize corona discharge through tungsten or silicon carbide emitters powered by AC, DC, or pulsed DC sources, with material selection balancing ionization efficiency against erosion resistance and particle generation characteristics.
Housing and structural components for ionization systems increasingly utilize specialized polymers that minimize outgassing while providing adequate insulation properties. High-performance systems incorporate PTFE, PEEK, or proprietary fluoropolymer composites that withstand constant ion bombardment without degradation or particle shedding. These advanced materials significantly outperform earlier generations of ionizers in terms of discharge times (typically achieving discharge reduction from 5000V to 500V in under 10 seconds) while maintaining ISO Class 3 or better cleanroom compatibility throughout their service life.
Ultra-clean room compatible ESD materials: PVDF and PEEK applications
Ultra-clean room environments (ISO Class 3 and cleaner) present extreme challenges for ESD material selection, requiring exceptional particle control while maintaining effective static protection. Polyvinylidene fluoride (PVDF) and polyether ether ketone (PEEK) have emerged as leading materials for these applications due to their unique combinations of cleanliness, chemical resistance, and ability to incorporate conductive networks without compromising structural integrity. These high-performance polymers form the foundation for many advanced ESD solutions in semiconductor front-end manufacturing.
PVDF-based materials offer excellent chemical resistance against the aggressive process chemicals used in semiconductor fabrication while providing low particle generation and outgassing characteristics. When compounded with controlled amounts of carbon nanotubes or conductive carbon black, PVDF can achieve surface resistivity in the 10⁶ to 10⁹ ohms/square range while maintaining ISO Class 2 compatibility. These materials typically serve in fluid handling components, wafer carriers, and containment systems where chemical exposure occurs alongside ESD risks.
PEEK applications focus primarily on high-temperature or high-mechanical-stress components within the semiconductor manufacturing environment. With heat deflection temperatures exceeding 300°C, conductive PEEK formulations maintain their protective properties through high-temperature processes where other materials would degrade. Advanced fiber-reinforced, carbon-loaded PEEK composites achieve remarkable combinations of mechanical strength, dimensional stability, and controlled conductivity (typically 10⁵ to 10⁸ ohms/square), making them ideal for precision component handling systems in advanced node fabrication processes.
Nano-composite materials in next-generation ESD protection
Nano-composite materials represent the cutting edge of ESD protection technology, incorporating precisely engineered structures at the nanometer scale to achieve previously impossible combinations of cleanliness, conductivity, and mechanical properties. These advanced materials typically utilize carbon nanotubes, graphene, nanofibers, or metallic nanoparticles dispersed within high-performance polymer matrices, creating three-dimensional conductive networks that require significantly lower filler loading compared to traditional composites.
Carbon nanotube (CNT) composites have demonstrated particular promise for semiconductor applications, achieving consistent conductivity with loading levels below 3% by weight compared to 15-20% required for traditional carbon black systems. This reduced loading maintains the base polymer's mechanical properties while significantly reducing particle generation and outgassing. Leading-edge formulations utilizing functionalized multi-walled carbon nanotubes can achieve temperature-stable resistivity values between 10⁴ and 10⁸ ohms/square while meeting or exceeding ISO Class 1 cleanliness requirements.
Implementation challenges for nano-composite materials include production scaling, consistency control, and cost management. Current manufacturing processes typically limit these materials to high-value applications where their performance advantages justify premium pricing. However, ongoing production technology advancements are gradually reducing implementation barriers, with industry analysts projecting broader adoption across semiconductor manufacturing within the next 3-5 years as production scales and costs decline. The exceptional performance characteristics of these materials make them particularly valuable for advanced node semiconductor fabrication, where device feature sizes below 5nm create unprecedented ESD sensitivity.
ESD material testing, certification, and compliance standards
Effective implementation of ESD protection materials requires rigorous testing and certification to verify performance against established standards. These processes provide manufacturers with confidence that materials will deliver expected protection levels while ensuring compatibility with production environments. A comprehensive testing program addresses both initial material qualification and ongoing verification throughout the material's service life, with particular attention to factors that could degrade performance over time.
The global nature of electronics manufacturing has driven substantial harmonization of ESD standards, with the ANSI/ESD S20.20 and IEC 61340 series achieving broad international recognition as defining frameworks for ESD control programs. These standards establish both performance requirements and testing methodologies for ESD protection materials, creating a common language for material specification and compliance verification across diverse manufacturing operations.
Beyond standard compliance, many manufacturers implement application-specific testing that addresses the unique requirements of their production environments. These customized protocols often evaluate material performance under actual usage conditions, including exposure to process chemicals, temperature cycling, mechanical wear, and other factors that might impact long-term protection reliability.
ANSI/ESD S20.20 material requirements and testing methodologies
The ANSI/ESD S20.20 standard provides a comprehensive framework for ESD control programs, including specific material requirements and testing methodologies to ensure protection effectiveness. This standard has been widely adopted across the electronics manufacturing industry, serving as the foundation for material specification and compliance verification in diverse production environments. For materials to comply with S20.20 requirements, they must demonstrate performance within specified parameters under standardized testing conditions.
Surface resistivity testing represents the primary evaluation method for most ESD materials, following procedures defined in ANSI/ESD STM11.11 and ANSI/ESD STM11.12. These tests utilize concentric ring electrodes or parallel bar electrodes applied to material surfaces under controlled pressure, with resistance measurements taken after specified voltage application periods. S20.20-compliant work surfaces must demonstrate surface resistivity between 10⁶ and 10⁹ ohms/square, while flooring systems are typically specified between 10⁶ and 10⁹ ohms/square to ground when measured with standardized footwear.
Charge generation testing evaluates the material's propensity to generate static charges through triboelectric contact with other materials. Following ANSI/ESD STM97.2 methodology, this testing measures voltage generation when materials separate after standardized contact periods. S20.20-compliant materials typically must generate less than 200 volts in these tests, with premium materials for semiconductor applications often achieving values below 50 volts. Additional material-specific tests may include groundability verification, resistance to ground measurements, and decay time testing depending on the material's intended application within the ESD control program.